Die Bestimmung des geeigneten Intervalls für den Austausch der Schraubenkompressorlager erfordert eine Kombination von Faktoren, einschließlich Betriebsbedingungen, Wartungshistorie und Leistungsüberwachung. Hier ist ein systematischer Ansatz:
Betriebsbedingungen: Die Betriebsumgebung eines Schraubenkompressors kann je nach Faktoren wie Branche, Anwendung, geografischem Standort und Umgebungsbedingungen stark variieren. Kompressoren, die auf Offshore-Öl- und Gasplattformen eingesetzt werden, stehen vor anderen Herausforderungen als Kompressoren, die in Industrieanlagen oder Produktionsanlagen betrieben werden. Durch die Analyse der Nuancen der Betriebsbedingungen kann das Wartungspersonal potenzielle Stressfaktoren identifizieren, die den Lagerverschleiß beschleunigen können, wie z. B. die Einwirkung korrosiver Gase, hohe Luftfeuchtigkeit oder häufige Starts und Stopps. Durch die Quantifizierung dieser Faktoren und ihrer Auswirkungen auf die Lagerleistung können Benutzer ihren Wartungsansatz so anpassen, dass spezifische Herausforderungen effektiv angegangen werden.
Wartungsverlauf: Eine gründliche Überprüfung des Wartungsverlaufs liefert wertvolle Einblicke in die Leistungstrends von Schraubenkompressorlagern im Laufe der Zeit. Es ermöglicht Benutzern, Fehlermuster, wiederkehrende Probleme oder unerwartete Abweichungen von erwarteten Leistungsmetriken zu erkennen. Durch die Analyse historischer Daten können Wartungsteams Wartungsaktivitäten mit der Gerätezuverlässigkeit und Betriebszeit korrelieren und so Bereiche für Verbesserungen und Optimierungen identifizieren. Durch die Nutzung historischer Wartungsaufzeichnungen können Benutzer proaktive Strategien zur Minderung bekannter Risiken, zur Verbesserung von Wartungspraktiken und zur Verlängerung der Lebensdauer kritischer Komponenten wie Lager entwickeln.
Leistungsüberwachung: Die Leistungsüberwachung beschränkt sich nicht auf regelmäßige Bewertungen, sondern umfasst die kontinuierliche Echtzeitüberwachung wichtiger Betriebsparameter. Moderne Schraubenkompressorsysteme sind beispielsweise mit Sensoren und Überwachungsgeräten ausgestattet, die zahlreiche Daten zu Variablen wie Vibrationsniveaus, Temperaturgradienten, Druckschwankungen und Energieverbrauch liefern. Durch den Einsatz fortschrittlicher Überwachungstechnologien und Datenanalysetools können Benutzer subtile Änderungen im Lagerverhalten erkennen, die auf einen drohenden Ausfall hinweisen können. Die Leistungsüberwachung in Echtzeit ermöglicht eine proaktive Entscheidungsfindung und ermöglicht es Wartungsteams, einzugreifen, bevor Probleme eskalieren und die Produktion beeinträchtigen.
Zustandsüberwachung: Die Zustandsüberwachung geht über herkömmliche Wartungsansätze hinaus und konzentriert sich auf die frühzeitige Erkennung abnormaler Betriebsbedingungen und beginnender Fehlerarten. Dazu gehört der Einsatz einer Reihe von Diagnosetechniken, darunter Vibrationsanalyse, Ölanalyse, Thermografie, Ultraschallprüfung und Überwachung akustischer Emissionen. Diese Techniken ermöglichen es dem Wartungspersonal, den Zustand der Lager von Schraubenkompressoren nicht-invasiv zu beurteilen und potenzielle Probleme zu identifizieren, bevor sie sich in katastrophalen Ausfällen manifestieren. Durch die Integration der Zustandsüberwachung in routinemäßige Wartungsabläufe können Benutzer ungeplante Ausfallzeiten minimieren, Wartungspläne optimieren und die Gerätezuverlässigkeit maximieren.
Risikobewertung: Die Risikobewertung ist ein systematischer Prozess zur Bewertung der Wahrscheinlichkeit und Folgen potenzieller Ausfallszenarien im Zusammenhang mit Schraubenkompressorlagern. Dazu gehört die Identifizierung von Gefahren, die Bewertung von Risiken, die Priorisierung von Abhilfemaßnahmen und die Entwicklung von Notfallplänen. Faktoren wie die Kritikalität der Ausrüstung, die Auswirkungen von Ausfällen auf Produktionsprozesse, Anforderungen zur Einhaltung gesetzlicher Vorschriften und Sicherheitsaspekte werden bei der Risikobewertung berücksichtigt. Durch die Quantifizierung von Risiken und ihren potenziellen Folgen können Benutzer Ressourcen effektiv zuweisen, Wartungsaktivitäten priorisieren und gezielte Eingriffe implementieren, um die Wahrscheinlichkeit von lagerbedingten Ausfällen zu verringern.
Screw Compressor Axial-Pendelrollenlager
Screw Compressor Axial-Pendelrollenlager
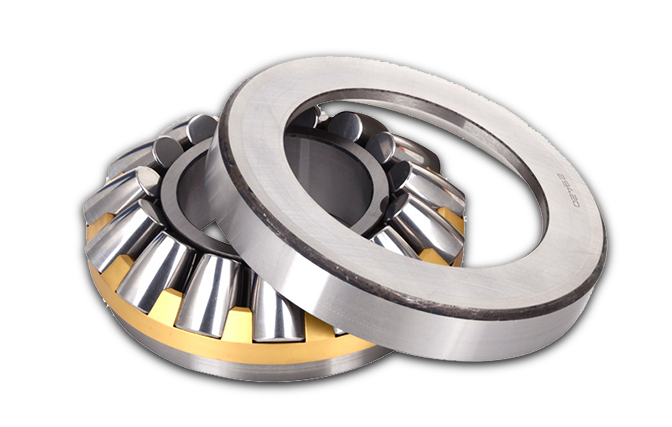
DHK-Axial-Pendelrollenlager sind in drei verschiedenen Konfigurationen erhältlich, die auf unterschiedlichen Abmessungen und Käfigkonstruktionen basieren.
Kleine und mittelgroße Pendelrollenlager können aus massivem Kupferkäfig (Nachsetzzeichen MB) oder gestanztem Stahlkäfig (Nachsetzzeichen J) bestehen.
Der Standardaufbau für große Pendelrollenlager ist ein massiver Kupferkäfig (Nachsetzzeichen MB).