Common failure modes or issues associated with Gepaarte einreihige Kegelrollenlager include:
1. Ermüdungsausfall: Verursacht durch wiederholte zyklische Belastung, die zur Bildung von Rissen in den Lagerkomponenten führt.
2.Oberflächenschäden: Aufgrund unzureichender Schmierung, Verschmutzung oder Fremdpartikel, die Abrieb oder Riefenbildung auf den Lageroberflächen verursachen.
3. Fehlausrichtung: Eine übermäßige Fehlausrichtung von Wellen oder Gehäusen kann zu ungleichmäßiger Belastung und vorzeitigem Verschleiß der Lagerrollen und Laufbahnen führen.
4. Überlastung: Das Aufbringen von Lasten, die über die Nennkapazität der Lager hinausgehen, kann zu plastischer Verformung oder zum Bruch von Lagerkomponenten führen.
5.Korrosion: Die Einwirkung korrosiver Umgebungen kann zu Lochfraß, Rost oder chemischem Abbau der Lageroberflächen führen und deren Leistung beeinträchtigen.
6.Unsachgemäße Installation: Falsche Installationsverfahren, wie z. B. unzureichende Vorspannung oder Fehlausrichtung während der Montage, können zu vorzeitigem Ausfall führen.
Um diese Probleme zu verhindern oder zu beheben, können die folgenden Maßnahmen ergriffen werden:
1. Ordnungsgemäße Wartung: Richten Sie ein zentrales Wartungsmanagementsystem ein, das Lagerwartungspläne in die Gesamtwartungspläne der Ausrüstung integriert. Dieses System sollte automatisierte Erinnerungen für Schmierung, Inspektionen und Austausch enthalten, die auf vorgegebenen Intervallen oder zustandsbasierten Auslösern basieren. Nutzen Sie fortschrittliche Wartungstechniken wie vorausschauende Wartung mithilfe von Algorithmen für maschinelles Lernen oder Fernüberwachungstechnologien, um die Wahrscheinlichkeit von Lagerausfällen vorherzusagen und Wartungsaktivitäten zu optimieren für maximale Geräteverfügbarkeit.
2. Korrekte Installation: Entwickeln Sie standardisierte Installationsverfahren mit detaillierten Schritt-für-Schritt-Anleitungen, kommentierten Diagrammen und Video-Tutorials, um den unterschiedlichen Qualifikationsniveaus des Wartungspersonals gerecht zu werden. Führen Sie nach der Installation Validierungsprüfungen mit Präzisionsmessgeräten wie Messuhren oder Laserausrichtungsgeräten durch, um die korrekte Wellenausrichtung, Lagervorspannung und den Sitz in der Gehäusebohrung zu überprüfen. Richten Sie einen funktionsübergreifenden Installationsüberprüfungsprozess ein, an dem Technik-, Wartungs- und Qualitätssicherungsteams beteiligt sind, um die Übereinstimmung mit technischen Spezifikationen und Best Practices der Branche sicherzustellen.
3. Effektive Schmierung: Führen Sie gründliche Schmierungsaudits durch, um die Schmierungspraktiken im gesamten Unternehmen zu bewerten und Bereiche mit Verbesserungspotenzial zu identifizieren, z. B. Schmierstoffauswahl, Anwendungsmethoden und Maßnahmen zur Kontaminationskontrolle. Implementieren Sie ein zentralisiertes Schmiermittelmanagementsystem mithilfe von RFID-Tags oder Barcode-Technologie, um den Schmiermittelverbrauch, Nachfüllpläne und die Gerätekompatibilität zu verfolgen, das Bestandsmanagement zu optimieren und das Risiko einer Fehlanwendung zu verringern. Arbeiten Sie mit Schmierstofflieferanten und Geräteherstellern zusammen, um Schmierstoffverträglichkeitstests durchzuführen und Schmierintervalle auf der Grundlage realer Betriebsbedingungen und Leistungsrückmeldungen zu optimieren.
4. Umweltschutz: Führen Sie Umweltrisikobewertungen durch, um potenzielle Kontaminationsquellen zu identifizieren, einschließlich Luftschadstoffen, Wassereintrittsstellen und chemischen Expositionspfaden, und entwickeln Sie gezielte, auf jede Risikokategorie zugeschnittene Minderungsstrategien. Investieren Sie in fortschrittliche Dichtungstechnologien wie Labyrinthdichtungen oder magnetische Lagerschutzvorrichtungen, die einen verbesserten Schutz vor eindringendem Wasser bieten, ohne die Lagerleistung oder die Wärmeableitungseigenschaften zu beeinträchtigen. Implementieren Sie strenge Sauberkeitsprotokolle für Wartungsaktivitäten, einschließlich der Verwendung spezieller Reinräume oder gefilterter Luftkammern für die Lagerung, Handhabung und Installation von Lagern, um das Eindringen von Verunreinigungen in kritische Lageroberflächen zu minimieren.
5. Überwachung und Inspektion: Setzen Sie eine umfassende Suite von Sensoren und Instrumenten zur Zustandsüberwachung ein, darunter Beschleunigungsmesser, Temperatursonden und Ölanalysesensoren, die strategisch positioniert sind, um Echtzeitdaten zu Lagerzustandsparametern und Leistungstrends zu erfassen. Integrieren Sie Zustandsüberwachungsdaten in Unternehmens-Asset-Management-Systeme oder cloudbasierte Analyseplattformen, um eine zentralisierte Datenaggregation, Visualisierung und Trendanalyse zu ermöglichen und so eine proaktive Entscheidungsfindung und Ressourcenzuweisung auf der Grundlage von Erkenntnissen zur vorausschauenden Wartung zu ermöglichen. Implementieren Sie Feedback-Mechanismen mit geschlossenem Regelkreis, die Zustandsüberwachungsdaten mit Auslösern für Wartungsmaßnahmen verknüpfen, wie z. B. der automatischen Generierung von Arbeitsaufträgen oder Befehlen zum Herunterfahren von Geräten, um ein rechtzeitiges Eingreifen als Reaktion auf auftretende Lagerverschleißprobleme sicherzustellen.
Gepaarte einreihige Kegelrollenlager
Gepaarte einreihige Kegelrollenlager
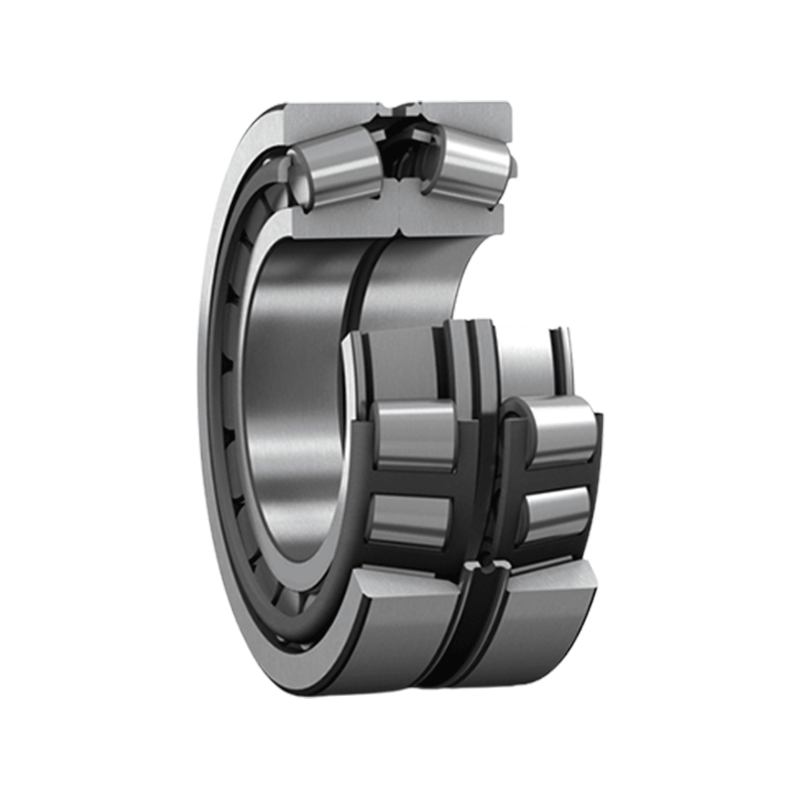